To supplement the rules there can be separate procedures which can be amended or added to without the need to rewrite the electrical safety rules. They can cover specific equipment on site such as maintenance, working on generators or chiller plant for instance, but the following are some examples of underpinning procedures for the safety rules.
- Permit to work system for work to be undertaken on the electrical system.
- Authorisation and assessment process for any electrical work by staff and contractors.
- Approval of electrical test equipment, tools and PPE.
- Live testing risk assessment procedure.
- Audit process for switchgear and control panels.
- Signs and labels for switchgear.
- Emergency procedures and first aid.
- Information, instruction, and training.
- Minor works and alterations.
There should also be local guidance written into the rules and procedures to help with interpretation and avoid ambiguity. The following flow chart Figure 6.2 shows the relationship between company policy, rules, procedures, and guidance.
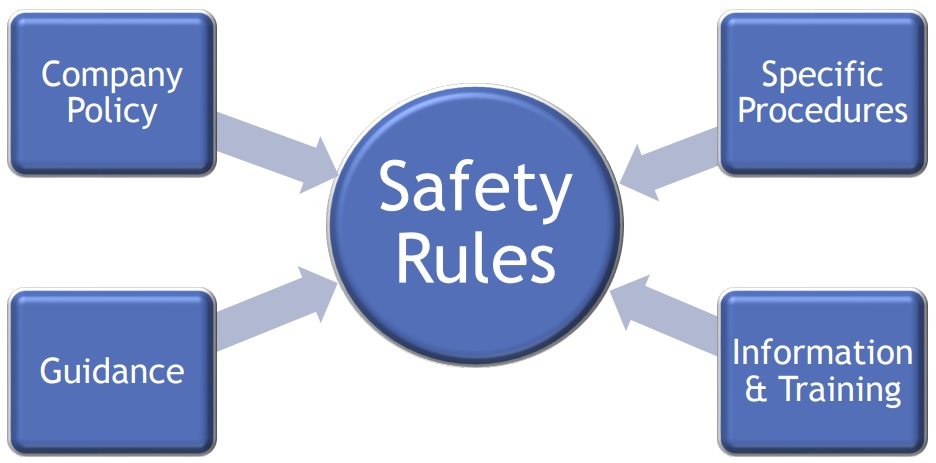
Figure 6.2
Safety rules and procedures with clear responsibilities are essential parts of a safe system of work. They should deal with properly assessing and authorising only competent people and should have systems for risk assessment. Where live working cannot be avoided, then the safe working systems should stipulate the use of the correct equipment and instruments. Electrical flashover accidents are very often caused by the operator dropping uninsulated tools or metal parts or by using incorrectly specified instruments. There should be a rule that no live work will be allowed on equipment that is damaged even for the reasons of proving dead. There have been many incidents involving damaged cables where an approach has been made to prove dead when the damaged cable was in fact still live.
6.3 Electrical Maintenance Program.
The main objective of an electrical maintenance program is to keep electrical equipment in good working condition so that it can reliably and safely operate within its design criteria. This includes testing and maintenance of circuit breakers, protective relaying and associated equipment on a regular basis. Improper maintenance of equipment can contribute to the severity of an arc flash. When a protective device such as a circuit breaker or relay is not properly maintained, the likelihood of it operating slower (or not at all) increases, which would also increase the duration of exposure to the arc flash. Although not technically part of an arc flash calculation study, a proper equipment maintenance program is vital in making sure the protective devices will operate correctly.
Maintenance inspections in particular can substantially impact on the control of arc flash risk with minimal additional effort in most cases. Visual inspections by competent individuals can pick up many defects that raise their own awareness of the hazard and reduce the likelihood of future accidents. In addition, good intelligence on vital assets can inform maintenance and replacement strategies.
In the case of control panels in industry, individuals interact with the equipment on a regular basis for production and breakdown purposes. Sometimes, it is these individuals who are responsible for the accumulation of defects that could lead to fatal electrical shocks and arc flash incidents. Issues such as forgetting to replace vital shrouds or fastenings or possibly allowing unauthorised temporary lash ups to become permanent can have fatal consequences for their colleagues at a later date. It is not just the individuals who are working inside the panels that create safety critical defects. I have worked extensively as an electrical safety consultant in the food industry with many household brands as well as presenting to the Institute of Occupational Safety and Health on the subject. Hygiene standards and electrical safety standards in the industry can sometimes conflict with one another. The need to ensure that production equipment is kept clean means routinely employing aggressive cleaning techniques using water jets and chemicals that often leading to water ingress into electrical equipment. To quote a food industry electrician “if a jumbo jet landed in our car park and we were asked to clean it – it would never fly again.”
The environmental conditions that commonly prevail in industrial production facilities means that design standards governing water/dust ingress and earthing/bonding must be of a high order. But, the first question a designer should ask is, does the electrical equipment (such as control panels) need to be in the high-risk production environment or can it be installed remotely?
All that said, duty holders must take a pragmatic view and for existing production lines it is not going to be possible to undertake any serious redesign of electrical systems. This is where routine inspections really come into their own. An audit process for switchgear and control panels, which is part of the electrical safety rules and procedures will have the effect of highlighting serious defects/omissions.
This can help inform risk assessments for future interactions and at one extreme, this may be to ban certain operations until improvements or replacements have been made.